パンチングメタルとは
パンチングメタルとは鉄などの金属の板に連続して孔を開けたもので、古くは打抜鋼板、また英語ではParforated Seatと呼ばれます。通常ではプレス機を用いて孔を開けており、使用する機械としては専用のパンチングプレス機やターレットパンチプレス(通称:タレパン)を使用して加工します。
〇φ×△P
通常パンチングメタルの仕様を言い表すときには上記のような言い方で表現されます。φは丸孔の直径、Pはピッチを表し、孔の中心から隣の穴の中心までの距離を表します。
例:3φ×5Pの場合
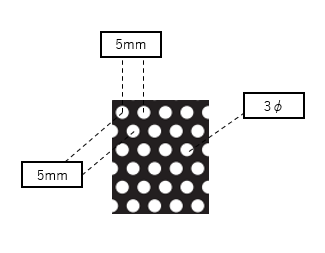
60度千鳥、45度千鳥、並列
パンチングメタルの仕様を表すものは上記の孔径×ピッチに加えて、配列パターンを表すとより正確に指定することができます。
60度千鳥
隣の孔と孔を結び合わせた際の内角が60度になる場合は60度千鳥と言います。もっとも一般的な仕様です。なお、60度千鳥の場合、縦と横ではピッチが異なり、90度反転させた場合は千鳥目が変わって見えますのでご注意ください。
45度千鳥

隣の孔と孔を結び合わせた角度が45度になる千鳥目のことを45度千鳥と言います。開孔率が60度千鳥と比べて高くなりますが、その分加工できない場合がございます。また、「角千鳥」という言い方もします。
並列
隣と隣の孔が縦横いずれも一直線に並ぶ仕様を並列と呼びます。開孔率は低いですが、孔が揃って並んでいるため外観部品などに使用されることが多いです。
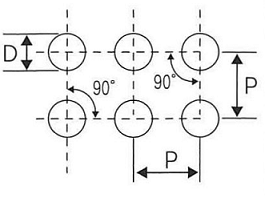
開孔率
板全体の面積に対しての開孔部の割合のことを言い、上記の孔径×ピッチや配列によって変わります。用途や要求仕様によって開孔率を選ぶことができます。
開孔率の計算については、こちらの開孔率自動計算のページで簡単に計算できますので、ご活用ください。
パンチングメタル加工に用いる機械について
切り板専用パンチングプレス
切り板素材をクランパーで掴み、X軸Y軸それぞれの方向に素材を動かすことによってパンチングを進める機械です。
最もオーソドックスで、古くから用いられる加工機械です。
フープ(コイル)材専用パンチングプレス
C型や門型プレスにフープ(コイル)の送り装置を付けることによってパンチング加工をする機械です。
コイル材は通常大きな重量でしか調達できませんが、ロットの大きい案件であれば、コイルは自動で材料を送ることができるため、工程の自動化が進み量産コストを下げることができます。
また、パンチング後にカッターを入れることによって切り板にできるほか、パンチング後に再びロールで巻き取ることによって、パンチングコイルを作ることもできます。
タレットパンチプレス
切り板を加工する機械ですが、こちらはタレットと呼ばれる円板に金型を多数配置することができるため、一度の加工で複数種類の穴があけられるほか、大板から製品を図面の寸法に切り出すこともパンチング加工と同時にできます。
一度の加工で複数種類の金型を使用できるほか、その機構を利用して製品を母材から切り出すこともできるため、少量多品種の受注に対応することで力を発揮します。
パンチングメタルに用いる素材について
鉄について
一番安価で手に入りやすい材料です。磁性を帯びており、また、さびやすいのが特徴です。その錆びやすい性質を解消するために表面処理(メッキ)を施すこともあり、主に亜鉛をメッキしたものを溶融亜鉛メッキ(SGCC・SGHC)、電気的にメッキ処理したものを電気メッキ(SECC・SEHC)、その他亜鉛メッキの耐食性を高めたものや、アルミメッキなど、用途・目的に応じてさまざまな種類の表面処理鋼板が存在します。
SPCC
冷間圧延(冷延)鋼板のこと。熱間工程後、常温まで冷ましたコイルを圧延することによって製作します。板厚は0.4mm~2.3㎜までが一般的で、板厚精度が高いため、主に薄板で精密板金などに使用されます。また、見た目が鈍く光ることから「ミガキ」などとも呼ばれます。材料表面には防錆用の油が塗布されているだけなのでさびやすいため、加工後にはメッキや塗装などの表面処理が必要です。
SPHC
熱間圧延(熱延)鋼板のこと。冷間工程を経る前の材料で、表面には酸化スケールが付着しているため、黒っぽい見た目となるため黒皮(くろかわ)とも呼ばれます。冷延工程を経ないため板厚精度は低いですが、単価は安く入手しやすいです。板厚は1.6㎜以上が中心となるため中厚板~厚板が中心となります。また、酸化スケールがプレス加工上では金型に悪影響を及ぼすため、リン酸処理を施したSPHC-Pがパンチング加工では頻繁に使用されます。こちらのSPHC-Pはその工程から「酸洗(さんせん)材」とも呼ばれます。こちらも加工後には塗装などの表面処理が必要です。
SGCC、SGHC
溶融亜鉛メッキ鋼板のこと。一般的に「トタン板」と呼ばれるものはこちらの鋼種のことを言います。メッキ母材が冷延鋼板か熱延鋼板かで名前が変わります。母材コイルを溶かした亜鉛の槽をを通すことによって母材表面にメッキします。メッキ厚が厚いため、錆に強い点が特徴です。昨今では材料メーカー各社でメッキ成分を工夫することによってより耐候性を高めるための工夫がされており、各社からより錆に強い高耐食溶融亜鉛メッキ鋼板がリリースされています。
SECC、SEHC
電気メッキ鋼板のこと。SGCCと同様にメッキ母材によって名前が変わります。母材コイルを溶かした亜鉛の槽に通すところはSGCCと同じですが、その際に電気処理を行うことによって、母材表面に亜鉛成分を析出させることによってメッキ加工を施します。メッキ厚はSGCCより薄いですが、強固な皮膜でありながら、亜鉛の投入量が減るため価格が安く、また、メッキ表面の精度が高く滑らかなため塗装性が高い点も特徴です。もちろん塗装なしでも使用されます。また、メッキ処理後の表面処理工程によって名前が異なり、クロメート処理をしたものをSECC-C、リン酸塩処理をしたものをSECC-Pといい、特に後者はその工程から「ボンデ鋼板」とも呼ばれ、昨今のクロームの環境負荷への配慮でボンデ鋼板の方が一般的に流通しています。
アルミについて
鉱物ボーキサイトを精錬したアルミナを原料とした材料で、さびにくく、また磁性も帯びておりません。純度の高い純アルミは柔らかく加工性が良いことが特徴ですが、そこに他の金属を混ぜた合金も種類が多く、その軽さという特徴に耐久性を持たせるなど、様々なバリエーションがあります。
A1100
純アルミ(アルミ比率99%以上)のこと。純度が高く、強度は低いですが、溶接性、加工性に優れます。そのため機能部品よりも外観部品などに使用されることが多く、手摺目隠しなどの建築金物などに多く使用されます。
A5052
アルミ―マグネシウム合金のこと。アルミ合金の中では中程度の強度を持つ合金で、アルミ板材の中では最も一般的な材料です。強度が高いため、プレス加工性は純アルミと比べて劣りますが、溶接性は高く、また、純アルミではできないレーザー加工も可能です。強度が高いため、機械カバーなどの強度が求められる場面でよく使われます。下二桁をとって「52(ゴーニ―)材」とも呼ばれます。
ステンレスについて
ステンレスの語源は「Stain Less」ということで、さびにくいことが特徴の材質で、ベースとなる鉄にニッケルやクロムなど、他の金属などを混ぜて製造します。また、JIS記号に基づいてSUS(サス)と呼ばれたりすることがありますが、こちらは”Steel Use Stainless”の略で、この後に数字などを付けて、鋼種を特定いたします。
SUS304
鉄をベースに約18%のクロムと、約8%のニッケルを配合した金属で、磁性は無く、さびにくいことが特徴です。世の中に出回っているステンレスの約7割がこのSUS304でステンレス鋼の中では最も広く普及している鋼種です。また、耐薬品性なども強いことが特徴です。
SUS316
鉄をベースに18%のクロムと12%のニッケル、さらにモリブデンを添加した金属で、SUS304よりも耐食性が高く、耐薬品性、耐海水性が高い金属です。主に化学分野などで使用されることが多い材質です。
SUS430
同じく鉄に約18%のクロムを配合した金属で、磁性があり、上記のSUS304よりもやや耐食性に劣ります。こちらも広く普及している鋼種の一つで、身の回りでは洋食器などで多く使用されています。
SUS409L
こちらも鉄をベースに11%のクロムに微量のチタン、さらに炭素を減らして作られた金属で、磁性があり、430に似て耐食性には劣りますが、耐熱性及び耐酸化性が高く、自動車などの内燃機のマフラーや発電所のサイレンサーなど、熱の発生する箇所で使用される鋼種です。ショウワでは最も多く使われる材質の一つです。
定尺について
例えば印刷用紙にA4 やB5といった規格のサイズがあるのと同じで、金属の材料にも規格のサイズ=定尺がございます。各鋼種によって定尺は異なりますので、ここで紹介いたします。
鉄(表面処理鋼板を含む)
914×1829(サブロク板)
1219×2438(シハチ板)
鉄の定尺の数字が中途半端なのはメートル法ではなく、尺貫法に準じた数字になっているため、中途半端な数字になっております。これは、近代製鉄技術が日本に取り入れられた当時、日本ではまだメートル法ではなく尺貫法が一般的であったためです。
ステンレス材(各鋼種共通)
1000×2000(メーター板)
1219×2438(シハチ板)
アルミ板
1000×2000(メーター板)
1250×2500(シハチ板)
アルミ材は、日本で生産技術が確立した時点でメートル法が一般的になっていたため、メートル法に準じた定尺寸法になったと言われています。なお、同じ「シハチ板」と呼ばれますが、鉄やステンレスとはサイズが異なります。
定尺寸法が決められると少ない使用量でも効率よく物を作ることができる反面、使用量が増えた場合、逆に歩留まりが悪くなってしまうということもございます。そのため数量が増えた場合には、定尺寸法に囚われない、特寸サイズでの発注も可能です。
二次加工について
曲げ加工
文字通り板を曲げる加工のことで、通常ベンディングプレス機(ベンダー)を使い、上下一組のヤゲンの間に板を挿入して、プレスすることにより、板を所定の形に曲げることができます。
ブランク加工
外形出しのこと。製品より一回り大きい板から外周を切り出し、製品を所定の形、大きさにする加工を言い、プレス機やタレットパンチプレス、レーザー加工機などを使用して加工することが可能です。
板巻き加工
板を丸めてパイプにする加工を言います。主な加工方法としては板をロール機に通して一気に丸める「ロール加工」と、プレス機と金型を使用し、いったんアルファベット”U”のような形に曲げた後、それをつぶして”O”の形にプレスする「UO加工」の2種類があり、それぞれ材質や板厚、ロットや製品の要求品質などによって工法を使い分けます。
シャーリング加工
金属の板を切断する際に、ハサミのように上刃と下刃の間で切断する加工のことです。通常はシャーリング機などを使用して加工します。
焼付塗装
金属を塗装する際に多く用いられる方法で、樹脂を含んだ塗料を母材に吹き付け、乾燥させた後、炉に入れて塗料を母材に定着させます。その加工工程は一般的には「2コート・1ベイク」と呼ばれ、下塗り・本塗りの2回の吹付と、1回の焼付で加工し、塗料も用途や要求品質に応じてウレタン樹脂、アクリル樹脂、フッ素樹脂など数種類から選択します。
アルマイト加工
アルミに対して行われる表面処理で、日本語では「陽極酸化処理」といいます。希硫酸などの処理液に、アルミを陽極として電気分解することによって、アルミ母材表面を強制的に電気化学的に酸化させることによって、耐酸化性、耐摩耗性を向上させることができます。また、処理時間によって色を変化させることができ、短ければシルバーなどの薄い色となり、長くすればブラックのような濃い色に変化させることができます。また、アルマイト加工後にさらにクリアを吹き付けることによってさらに耐候性を高めることができます。
レベラー加工
金属板をパンチングや切断をすると製品に反りが発生しますが、そちらを解消するための加工です。上下それぞれ複数のローラーの間に製品を通すことによって、パンチング工程などで製品に蓄積した応力(ストレス)を均一にし、反りを解消します。